A new age in solid timber processing
At Hutig we use a precision CNC band saw to cut prime grade solid timber into a heavy sawn veneer (and other sections) which is then permanently bonded to either: solid timber, birch plywood or poplar plywood. The choice of substrate depends on the mechanical and other requirements of the finished component. Get in touch to discuss specifications for bespoke solutions to meet your creative requirements.
Flexible engineering of timber
Using sawn veneer cut with a precision band saw gives us complete control over timber selection and enables the manufacture of components not possible using other timber processing methods – as in this picture showing 600mm wide book-matched quarter sawn oak for wall panelling.
Lighter handling and fitting
Poplar plywood is sustainably grown and harvested in Italy and Spain for the furniture, transport and packaging industries. This plywood is much lighter than birch plywood and has some amazing mechanical properties. We use this material extensively for core material where good mechanical strength, flexibility and low weight is important.
Reliable mechanics
Birch plywood is used as a core material where additional mechanical strength is required or where extra strong screw fixings are critical – e.g. interior door frames for hinge/frame fixings.
Any thickness or width of panel
This is a good example of poplar plywood being used as a core material for a 30mm thick furniture carcase/worktop or stair/Joinery components.
This construction benefits over laminated solid timber sections as consistency and mix of grain patterns are easier to control.
Mechanical stability is also guaranteed.
Long runs of material with total consistency
This section of skirting uses a 15mm poplar plywood core with a solid timber profiled edge and 2mm ash sawn face veneer (brushed).
This unique combination of materials and construction means there will be no rejected material on site; it is lightweight and easy to handle and extremely flexible making fitting easier. It is also resistant to humidity.
Normally supplied pre-finished and is batched to provide consistency of appearance.
Fool proof joinery packages expertly manufactured
We have also developed some products to save time and snagging on site like our composite architraves. The large picture shows the architrave prior to assembly.
These are normally supplied as a complete package with the door and all ironmongery pre-fitted etc and all pre-finished. We also fit acoustic seals/buffers to the door stops so there is no play or rattling on closing the door – positive, solid, quality.
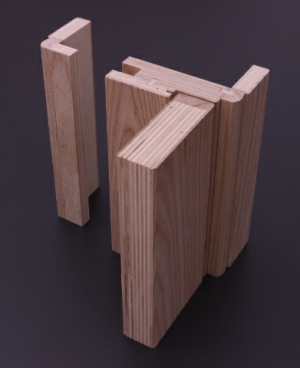
Composite architrave showing slip facing
Tradesman friendly solutions
The architrave frame fixings are all hidden behind the door stops. The stops are planted on with a full locating tongue & groove joint (glued). This means no patching up holes etc afterwards.
A tailored slip facing is inserted (glued) into the frame to complete the job.
A new benchmark in quality
Example of engineered interior door – 36mm poplar plywood core; 2.5mm ash sawn veneer (brushed); chamfered edges.
As can be seen in the detailing here it’s not possible to tell whether this is solid timber or sawn veneer construction.
The main thing that stands out is the quality of the textured surface and the timber selection – a result of precision band sawing.
A new world of creativity and longevity
Expert manufacture and tight quality control means you will have more time to manage your project – and endless possibilities to design creative interiors.
So why not include a discussion with Hutig early in the design process to optimise the technology and the way you could exploit our deliverable solutions. Please don’t hesitate to contact us to discuss your project!